How to Clean and Maintain Your Knife Magnet Strip
By:Admin
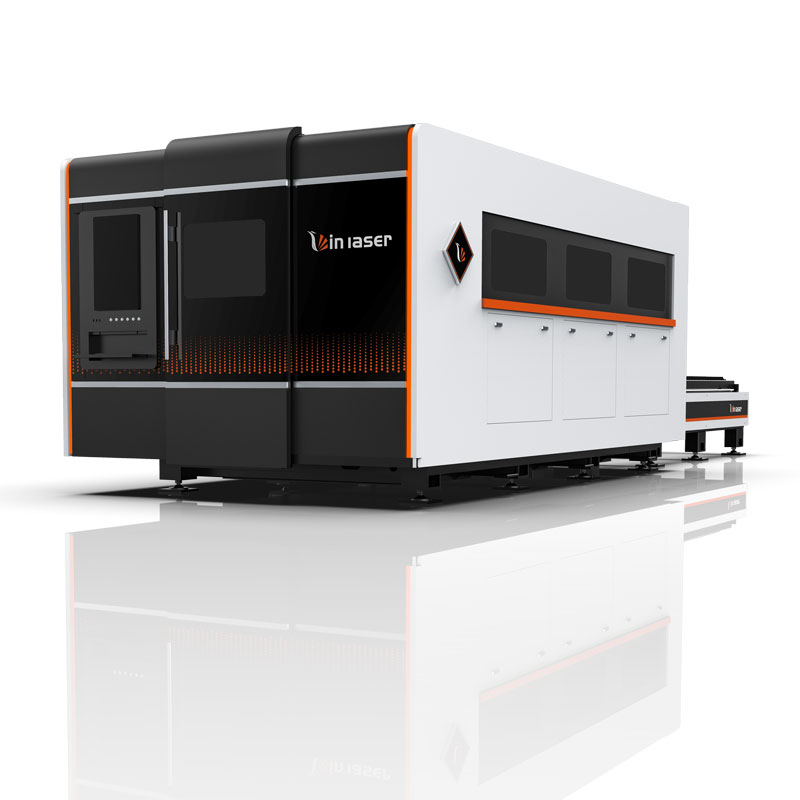
Slag buildup is a common issue in metal processing facilities, where high temperatures and rapid cooling can lead to the formation of hard, stubborn slag on the surface of knife strips. This buildup can significantly reduce the cutting efficiency and accuracy of the tools, leading to increased downtime and maintenance costs. The new Knife Strip De-Slagging technology from {} is set to address this problem and provide a comprehensive solution for metal processing facilities.
The innovative technology utilizes a combination of high-pressure water jets and advanced cleaning agents to effectively remove slag from knife strips, without causing any damage to the cutting edges or the underlying material. This ensures that the knife strips are thoroughly cleaned and restored to their original condition, resulting in improved cutting performance and extended tool life.
In addition to its powerful cleaning capabilities, the Knife Strip De-Slagging technology also offers a number of key benefits for metal processing facilities. By removing slag buildup from knife strips, the technology helps to minimize the risk of defects and imperfections in the finished products, resulting in higher quality output and increased customer satisfaction. Furthermore, the improved cutting efficiency and longevity of the tools can lead to significant cost savings for the facility, as well as reduced maintenance and replacement expenses.
"We are thrilled to introduce our new Knife Strip De-Slagging technology to the metal processing industry," said a spokesperson for {}. "This innovative solution is the result of extensive research and development, and we are confident that it will deliver substantial benefits for our customers. By effectively removing slag buildup from knife strips, our technology is set to enhance the performance and durability of cutting tools, ultimately improving the productivity and profitability of metal processing facilities."
The introduction of the Knife Strip De-Slagging technology further solidifies {}'s position as a leader in the industrial cutting tools industry. With a strong commitment to innovation and customer satisfaction, the company continues to develop and introduce cutting-edge solutions that address the evolving needs of the metal processing industry. The new technology is set to offer a competitive edge to metal processing facilities, enabling them to achieve higher levels of efficiency, quality, and cost-effectiveness in their operations.
As metal processing facilities around the world strive to enhance their productivity and competitiveness, the Knife Strip De-Slagging technology from {} presents a compelling opportunity to achieve these goals. By investing in this innovative solution, facilities can benefit from improved cutting performance, reduced maintenance costs, and enhanced product quality, ultimately leading to greater success and profitability in the highly competitive metal processing industry.
With the introduction of the Knife Strip De-Slagging technology, {} continues to demonstrate its commitment to driving positive change and innovation within the industrial cutting tools industry. This latest offering is poised to make a significant impact on metal processing facilities, helping them to overcome the challenges associated with slag buildup and achieve higher levels of efficiency, quality, and profitability in their operations.
Company News & Blog
Revolutionary Hydraulic Bending Technology Set to Transform Manufacturing Processes" became "Groundbreaking Hydraulic Bending Technology Poised to Revolutionize Manufacturing Procedures
Hydraulic Bending Technology Takes the Manufacturing Industry by StormThe rise of industrialization has brought about a heightened demand for efficiency, accuracy, and speed when it comes to manufacturing. Companies are continually searching for ways to streamline their production processes and increase output without compromising quality. The latest trend that has taken the manufacturing industry by storm is hydraulic bending technology.Hydraulic bending technology is a process that utilizes hydraulic-powered machines to bend and shape sheet metal. This technique is a significant improvement over traditional methods that require manual labor and extensive fabrication. With hydraulic bending technology, companies can now produce high-quality and precision-engineered parts that are essential for various applications such as construction, automotive, and aerospace industries.One of the leading companies providing hydraulic bending technology is {remove brand name} technology. Started in 1982, {remove brand name} has been specializing in the design and manufacturing of hydraulic bending machines and other related equipment.Their hydraulic bending machines are designed to perform various bending and forming operations on metals such as aluminum, stainless steel, and carbon steel. One of the key features of these machines is the ability to provide great accuracy and repeatability. This aspect is essential when it comes to ensuring high-quality products because even a slight deviation from the desired measurements can render the product defective.{remove brand name} also provides custom solutions to meet the specific needs of their clients. This aspect of their service gives manufacturers the ability to produce unique products that require specialized bends and shapes. Additionally, the company's machines are fitted with advanced control systems that allow the operators to adjust the speed, torque, and other variables during the bending process, ensuring excellent results.Another notable advantage of hydraulic bending technology is the reduction in material waste. With traditional methods, the fabrication process can result in the production of excess scrap metal. This wastage not only results in the loss of raw materials but also increases production costs. However, with hydraulic bending machines, operators can reduce scrap metal to a bare minimum, consequently, reducing production costs.Moreover, hydraulic bending technology provides increased safety for operators. Unlike traditional methods, where operators need to employ brute force, hydraulic bending machines provide a more controlled process. Furthermore, the machines come with safety features such as emergency stops and guards, ensuring that the operators are safe while performing their tasks.In conclusion, hydraulic bending technology is a significant advancement that has revolutionized the manufacturing processes, making them efficient, safe, and cost-effective. The technology's precision and repeatability ensure the creation of high-quality products, while the reduction in waste and increased safety make it a valuable tool in the manufacturing industry.{remove brand name} technology remains at the forefront of providing hydraulic bending solutions to various industries. With their custom solutions, advanced control systems, and expert technical know-how, the company has been helping manufacturers optimize their production processes and achieve their specific goals. Their dedication to customer satisfaction and providing quality solutions has undoubtedly earned them a place in the global manufacturing technology market.
High Precision Laser Tube Cutting Machine for CNC Applications
CNC Laser Tube Cutting Machine Revolutionizes Manufacturing IndustryWith the advancement of technology, many industries have shifted towards automation and precision. The manufacturing industry is no exception, as it has been greatly influenced by the introduction of CNC laser tube cutting machines. These machines have revolutionized the production process by offering efficiency, accuracy, and flexibility in cutting a variety of materials.The CNC laser tube cutting machine is a high-tech piece of equipment that uses a powerful laser to cut through materials such as steel, aluminum, and other metals with extreme precision. The machine is controlled by a computer program that guides the laser to make intricate cuts and shapes, resulting in accurate and consistent products.One of the leading manufacturers of CNC laser tube cutting machines, {} has been at the forefront of this innovative technology. Their machines are known for their cutting-edge features, such as high-speed cutting, automatic loading and unloading, and advanced software for precise design and cutting. These machines are widely used in various industries, including automotive, aerospace, and construction.The introduction of CNC laser tube cutting machines has brought about significant changes in the manufacturing industry. One of the key advantages of these machines is their ability to produce complex and intricate designs with incredible speed and precision. This has allowed manufacturers to improve their production efficiency and reduce the time and cost associated with traditional cutting methods.Furthermore, CNC laser tube cutting machines have also enabled manufacturers to increase their production capacity and flexibility. With the ability to quickly switch between different cutting processes and materials, these machines have made it easier for companies to adapt to changing market demands and produce a wide range of products with minimal downtime.In addition to these benefits, CNC laser tube cutting machines have also led to improvements in the overall quality of products. The precision and accuracy of the laser cutting process result in clean, smooth edges and tight tolerances, making it possible to produce high-quality parts and components with minimal waste.The introduction of CNC laser tube cutting machines has not only transformed the way products are manufactured but has also had a positive impact on the environment. With their ability to cut materials with high precision and minimal waste, these machines have helped reduce the amount of scrap and material usage, leading to a more sustainable and eco-friendly manufacturing process.In conclusion, the introduction of CNC laser tube cutting machines has brought about significant advancements in the manufacturing industry. These machines have revolutionized the production process by offering efficiency, accuracy, and flexibility in cutting a variety of materials. With their cutting-edge features and benefits, CNC laser tube cutting machines have become an invaluable asset for manufacturers looking to improve their production processes and stay ahead in a competitive market.As the demand for high-quality products and efficient production methods continues to grow, CNC laser tube cutting machines are expected to play a crucial role in shaping the future of manufacturing. With continuous innovation and advancements in technology, these machines will undoubtedly continue to revolutionize the industry and drive further growth and development in the years to come.
Top Trends and Growth Opportunities in the Machine Tool Industry
The machine tool industry is a critical element of modern manufacturing, providing the equipment necessary for a range of machining and metalworking processes. These machines are essential for producing a wide variety of products, from automobiles and aircraft to consumer electronics and medical devices. As such, the machine tool industry plays a vital role in supporting the global economy and driving technological advancements.One company at the forefront of this industry is {}. Founded in 1985, {} has established itself as a leading manufacturer of advanced machine tools, offering a comprehensive range of products for various industrial applications. With a strong focus on research and development, {} has continuously pushed the boundaries of innovation, delivering cutting-edge solutions to meet the evolving needs of the manufacturing sector.In recent years, the machine tool industry has experienced significant growth, driven by the increasing demand for high-precision components and the adoption of advanced manufacturing technologies. The relentless pursuit of efficiency, accuracy, and automation has led to a surge in investments in state-of-the-art machine tools, spurring further development and expansion within the industry.One of the key drivers of this growth has been the global push for industrial modernization and the rise of smart manufacturing. As factories seek to enhance their productivity and adaptability, there has been a growing reliance on advanced machine tools that offer superior performance, flexibility, and connectivity. This trend has paved the way for a new era of digital manufacturing, characterized by the integration of robotics, artificial intelligence, and data analytics into machine tool systems.In response to these market dynamics, {} has continuously refined its product offerings, introducing a range of cutting-edge machine tools that are tailored to the needs of modern manufacturers. The company's portfolio includes precision CNC machining centers, turning centers, and multitasking machines, all of which are designed to deliver exceptional levels of accuracy, speed, and efficiency. Furthermore, {} has embraced the principles of industry 4.0, incorporating smart technologies and digital capabilities into its machines to enable seamless integration with the broader manufacturing ecosystem.Moreover, in recognition of the increasing importance of sustainability in manufacturing, {} has also prioritized the development of eco-friendly machine tools. By leveraging energy-efficient technologies and optimizing the use of resources, the company is committed to reducing the environmental impact of its products while helping its customers achieve their sustainability goals.With a strong global presence, {} has established a solid reputation for delivering high-quality machine tools that cater to diverse industrial sectors, including aerospace, automotive, medical, and general engineering. The company's dedication to innovation, reliability, and customer satisfaction has earned it a loyal clientele and positioned it as a trusted partner for manufacturing businesses worldwide.Looking ahead, the machine tool industry is expected to continue its upward trajectory, driven by the ongoing advancements in manufacturing processes and the growing demand for customized, high-quality products. As the industry evolves, the role of machine tools will become even more pivotal, enabling manufacturers to stay competitive in an increasingly dynamic and demanding market environment.In conclusion, the machine tool industry is a cornerstone of modern manufacturing, and companies like {} are playing a crucial role in shaping its future. With a steadfast commitment to innovation, quality, and sustainability, {} is well-positioned to lead the way in delivering the next generation of machine tools that will drive the industry forward into a new era of productivity and progress.
Ultimate Guide to Laser Cutting Machines for Precision Plate Cutting
Title: Advanced Plate Laser Cutting Machine Revolutionizes Metal Fabrication IndustryIntroduction:In today's rapidly evolving technology landscape, innovative solutions are continuously emerging to enhance various industries' efficiency and productivity. In line with this trend, the introduction of an advanced Plate Laser Cutting Machine has taken the metal fabrication industry by storm. This cutting-edge technology is set to revolutionize the way metal components are manufactured, ultimately redefining the sector's capabilities and setting new standards of precision and quality.Product Overview and Features:The Plate Laser Cutting Machine is a state-of-the-art equipment designed to provide reliable and efficient cutting solutions for a wide range of metal plates. With its precision laser cutting technology, this machine can seamlessly cut through various metals, including steel, aluminum, copper, and stainless steel, among others. The machine is equipped with a powerful laser source, efficient cooling systems, and intelligent automation features, making it an indispensable asset for metal fabrication companies seeking enhanced output.Key Features of the Plate Laser Cutting Machine include:1. High Precision Cutting: The laser cutting technology employed by this machine ensures exceptional precision, allowing intricate designs and complex shapes to be accurately reproduced in a variety of metal plates.2. Versatile Applications: The machine's flexibility enables it to be used in numerous industries, such as automotive, aerospace, construction, and electronics. It can effortlessly handle demanding cutting tasks, whether it is creating intricate components or executing mass production requirements.3. Efficiency and Speed: The Plate Laser Cutting Machine significantly reduces production time and effort due to its fast cutting speed and automated features. This ensures optimal productivity for metal fabricators and enables them to meet tight project deadlines with ease.4. Enhanced Safety: Incorporated safety mechanisms prioritize the protection of operators and workers using the machine. The machine features automated safety guards, real-time monitoring, and emergency stop functions, ensuring a secure working environment.Benefits to the Metal Fabrication Industry:The introduction of the Plate Laser Cutting Machine marks a significant milestone in the metal fabrication industry. Its cutting-edge features offer several advantages, including:1. Improved Product Quality: The machine's high precision and accuracy guarantees flawless cuts, reducing the need for extensive post-processing and improving overall product quality.2. Streamlined Workflow: The automated features of the machine streamline the manufacturing process by reducing human intervention. This boosts efficiency and allows fabricators to allocate their resources more effectively.3. Cost Savings: The cutting-edge machine optimizes material usage, reducing waste and minimizing production costs. Additionally, its high-speed performance enhances productivity, effectively lowering labor expenses.4. Design Freedom: The Plate Laser Cutting Machine enables the production of complex designs and shapes with ease, empowering manufacturers with greater design freedom and flexibility, ultimately leading to more innovative and unique products.Company Overview:The manufacturer of the Plate Laser Cutting Machine is a highly reputable technology company committed to developing cutting-edge industrial solutions. With extensive experience and expertise, the company has consistently delivered innovative products that redefine the capabilities of various industries.Conclusion:The advanced Plate Laser Cutting Machine has heralded a significant breakthrough in metal fabrication, revolutionizing the industry by setting new benchmarks in precision cutting, speed, and overall quality. With its versatile applications and exceptional features, this cutting-edge technology is poised to reshape the metal fabrication landscape, empowering manufacturers to unlock increased productivity, efficiency, and design freedom.
How to Clean and Maintain Your Knife Magnet Strip
Toledo, OH - The leading manufacturer of industrial cutting tools, {}, has announced the introduction of a new Knife Strip De-Slagging technology that promises to revolutionize the metal processing industry. This groundbreaking technology is designed to efficiently and effectively remove slag buildup from knife strips, ensuring optimal performance and longevity of the cutting tools.Slag buildup is a common issue in metal processing facilities, where high temperatures and rapid cooling can lead to the formation of hard, stubborn slag on the surface of knife strips. This buildup can significantly reduce the cutting efficiency and accuracy of the tools, leading to increased downtime and maintenance costs. The new Knife Strip De-Slagging technology from {} is set to address this problem and provide a comprehensive solution for metal processing facilities.The innovative technology utilizes a combination of high-pressure water jets and advanced cleaning agents to effectively remove slag from knife strips, without causing any damage to the cutting edges or the underlying material. This ensures that the knife strips are thoroughly cleaned and restored to their original condition, resulting in improved cutting performance and extended tool life.In addition to its powerful cleaning capabilities, the Knife Strip De-Slagging technology also offers a number of key benefits for metal processing facilities. By removing slag buildup from knife strips, the technology helps to minimize the risk of defects and imperfections in the finished products, resulting in higher quality output and increased customer satisfaction. Furthermore, the improved cutting efficiency and longevity of the tools can lead to significant cost savings for the facility, as well as reduced maintenance and replacement expenses."We are thrilled to introduce our new Knife Strip De-Slagging technology to the metal processing industry," said a spokesperson for {}. "This innovative solution is the result of extensive research and development, and we are confident that it will deliver substantial benefits for our customers. By effectively removing slag buildup from knife strips, our technology is set to enhance the performance and durability of cutting tools, ultimately improving the productivity and profitability of metal processing facilities."The introduction of the Knife Strip De-Slagging technology further solidifies {}'s position as a leader in the industrial cutting tools industry. With a strong commitment to innovation and customer satisfaction, the company continues to develop and introduce cutting-edge solutions that address the evolving needs of the metal processing industry. The new technology is set to offer a competitive edge to metal processing facilities, enabling them to achieve higher levels of efficiency, quality, and cost-effectiveness in their operations.As metal processing facilities around the world strive to enhance their productivity and competitiveness, the Knife Strip De-Slagging technology from {} presents a compelling opportunity to achieve these goals. By investing in this innovative solution, facilities can benefit from improved cutting performance, reduced maintenance costs, and enhanced product quality, ultimately leading to greater success and profitability in the highly competitive metal processing industry.With the introduction of the Knife Strip De-Slagging technology, {} continues to demonstrate its commitment to driving positive change and innovation within the industrial cutting tools industry. This latest offering is poised to make a significant impact on metal processing facilities, helping them to overcome the challenges associated with slag buildup and achieve higher levels of efficiency, quality, and profitability in their operations.
Understanding the Different Classes of Lasers for Safe Use
Laser Classification System Enhances Safety and Productivity Across IndustriesLasers are used in a variety of industries for tasks ranging from cutting and welding to marking and engraving. Though these devices have proven remarkably useful in a vast array of applications, they also present potential dangers to human beings and the environment. Laser Classification is an important aspect to ensure safety in workplaces, especially in industries that rely heavily on lasers.Laser Classification involves the categorization of lasers into different classes based on their potential dangers, with each class assigned its own set of safety guidelines and requirements. Class 1 lasers present no hazard, while Class 2 lasers are low-power and can cause eye damage if viewed directly for extended periods without eye protection. Class 3 and 4 lasers, on the other hand, pose significant risks, such as skin and eye injuries, burns and potential fire hazards. The proper classification of laser devices is essential to ensure the safety of people and effective operation of such equipment in the workplace.A leading provider of laser technology has introduced a comprehensive Laser Classification System, designed to enhance workplace safety, productivity, and regulatory compliance in a broad range of industries. The company's LCD touch-screen interface and automated software system classify the laser, ensuring that the device is being used safely and in compliance with regulatory guidelines."We understand the importance of providing our customers with safe, efficient, and reliable laser technology," said the company's CEO. "With our new Laser Classification System, we are not only ensuring safety, but we are also streamlining the entire classification process, allowing our customers to focus on their critical applications."The system automatically performs a series of tests, including measurement of output power, wavelength, pulse duration, and beam divergence, to accurately measure the laser's safety classification. Based on the results, the system assigns the appropriate classification according to the international safety standards and regulations, saving time and reducing the likelihood of human error in the classification process.In addition to offering a more efficient classification process, the system provides access to detailed reports and data, including the laser's classification and specifications. The data is automatically stored and can be easily retrieved for auditing and regulatory compliance purposes. This not only simplifies the classification process but also makes it easier to maintain safety records and facilitate the disposal or reclassification of devices when necessary.The Laser Classification System has been well-received by professionals across multiple industries, from aerospace to medical device manufacturing. In the aerospace industry, lasers are used for cutting and welding aircraft components and structures. With the implementation of the Laser Classification System, engineers and technicians can now work with confidence knowing that their laser devices are properly classified and safe to use. "The new system has made laser classification much more user-friendly, and we are pleased to have our lasers registered and certified in compliance with international standards," said the operations manager of an aircraft components manufacturer. "This has significantly reduced our regulatory compliance workload and has streamlined our laser device inventory management."Likewise, in the medical device industry, lasers are used for a broad range of procedures, from cutting and ablating tissue to sealing blood vessels. Effective laser classification is essential to ensuring the safety of patients and the healthcare professionals who use the devices. With the Laser Classification System in place, medical device manufacturers can now ensure that their laser products are properly classified in accordance with the international safety regulations.In conclusion, the introduction of Laser Classification System by a leading provider of laser technology is a significant achievement, providing reassurance to industries that rely on lasers that they are using this equipment safely and in compliance with regulations. This automation of the laser classification process not only simplifies it but also enhances workplace safety, productivity, and regulatory compliance across multiple industries. The Laser Classification System is an example of how technology can solve existing problems and create a safer working environment for professionals.
High-Powered 6000w Laser Technology Making Waves in Industry
The laser cutting industry is experiencing a technological revolution with the introduction of the new Laser 6000w. This groundbreaking machine, developed by a leading company in the laser technology industry, is set to redefine the standards of precision cutting and efficiency.With a cutting power of 6000 watts, this cutting-edge laser machine is capable of handling a wide range of materials with unparalleled accuracy and speed. Whether it's metal, plastic, wood, or other industrial materials, the Laser 6000w delivers precise and clean cuts, making it an essential tool for various industries, including automotive, aerospace, and manufacturing.The company behind this innovation is known for its commitment to pushing the boundaries of laser technology. With years of experience and expertise, they have established themselves as a pioneer in the industry, constantly striving to develop cutting-edge solutions that cater to the evolving needs of their clients.The Laser 6000w is a testament to the company's dedication to innovation and excellence. Equipped with advanced features and a user-friendly interface, this machine offers unmatched versatility and performance. Its high-speed cutting capabilities enable it to tackle complex designs and intricate patterns with ease, while its precision ensures consistently high-quality results.In addition to its impressive cutting capabilities, the Laser 6000w is also designed with efficiency in mind. With its energy-efficient operation and minimal maintenance requirements, this machine offers a cost-effective solution for businesses looking to streamline their production processes and maximize their output.Furthermore, the company's commitment to customer satisfaction is reflected in the comprehensive support and service offerings that accompany the Laser 6000w. From installation and training to ongoing maintenance and technical support, the company ensures that their clients can harness the full potential of this cutting-edge technology.The introduction of the Laser 6000w is expected to have a significant impact on the laser cutting industry. With its unrivaled cutting power and efficiency, this machine has the potential to revolutionize the way materials are processed and fabricated, setting new standards for precision and productivity in the manufacturing sector.In conclusion, the Laser 6000w represents a significant milestone in the evolution of laser technology, and it is poised to make a lasting impact on the industry. With its advanced features, precision cutting capabilities, and commitment to customer satisfaction, this machine is set to elevate the standards of excellence in the world of laser cutting. The company's dedication to innovation and their track record of delivering cutting-edge solutions positions them as a leader in the industry and sets the stage for a new era of unparalleled efficiency and precision in material fabrication.
Discover the Affordability of Laser Cleaning Machines
Title: Cutting-Edge Laser Cleaning Technology Revolutionizes Industrial Cleaning ProcessesIntroduction:In recent years, the demand for innovative and efficient cleaning solutions has been steadily increasing across various industries. Traditional cleaning methods often involve the use of chemicals or abrasive techniques, which can be time-consuming, costly, and harmful to the environment. However, with the advent of laser cleaning technology, a new era of industrial cleaning has dawned. In this article, we will explore laser cleaning machines' cost-effective and eco-friendly benefits, paving the way for greater efficiency and sustainability in industrial cleaning processes.Cost-Effective Solution:Laser cleaning machines have emerged as a cost-effective alternative to conventional cleaning methods. Unlike traditional techniques that require the procurement of chemicals, specialized tools, or repeated replacement of consumables, laser cleaning machines offer significant long-term cost savings. While the initial investment may seem higher, laser cleaning machines eliminate the need for ongoing expenses, such as purchasing cleaning agents and replacing abrasive materials. Additionally, their high precision ensures minimal material loss, making them an economical choice for industries seeking enhanced cleaning efficiency.Environmentally Friendly Approach:Environmental consciousness has become a prominent consideration for companies worldwide. Laser cleaning machines brilliantly address this concern by providing an environmentally friendly cleaning alternative. Traditionally, industrial cleaning methods have resulted in the release of harmful chemicals, gases, or by-products into the environment. On the contrary, laser cleaning technology employs a non-contact and non-abrasive process, eliminating the need for toxic cleaning agents. By utilizing focused laser beams, these machines efficiently remove contaminants without generating hazardous waste, making them a sustainable choice for businesses committed to reducing their ecological footprint.Enhanced Safety and Precision:One of the key advantages of laser cleaning machines is their ability to operate with high precision and safety standards. From delicate historical artifacts to intricate machinery parts, laser cleaning offers a gentle and non-invasive cleaning approach. By adjusting various parameters, such as power density, pulse width, and spot size, operators can tailor the laser cleaning process to suit specific cleaning requirements, ensuring optimal results without damaging the surface being treated. This level of precision and control minimizes the risk of accidental damage that is more commonly associated with traditional cleaning methods.Versatility Across Industries:The versatility of laser cleaning machines allows them to be employed across a wide range of industries. Companies in automotive, aerospace, electronics, cultural heritage preservation, and many other sectors can benefit from the efficiency and effectiveness of this technology. Laser cleaning machines can remove rust, paint, corrosion, oil, and other contaminants from metal, stone, concrete, or delicate surfaces without compromising structural integrity or aesthetic appeal. This versatility has positioned laser cleaning as an invaluable tool in maintaining high cleanliness standards in diverse industrial applications.Company Introduction {}:With extensive expertise in the field, our company has become a leading provider of laser cleaning machines. Committed to innovation, we have developed cutting-edge technology that has set new industry standards. Our laser cleaning machines are designed to deliver outstanding performance, addressing the most challenging cleaning tasks with precision and efficiency. Moreover, our team of experts is dedicated to providing comprehensive support, offering training, and guiding our customers in maximizing the benefits of laser cleaning technology. As a trusted partner, we strive to ensure customer satisfaction by delivering cost-effective and eco-friendly solutions tailored to their unique cleaning requirements.Conclusion:Laser cleaning machines have emerged as revolutionary tools in the domain of industrial cleaning. By offering a cost-effective, environmentally friendly, and precise alternative to conventional cleaning methods, laser cleaning technology is transforming various industries. With their ability to remove contaminants efficiently without harming the material being cleaned, laser cleaning machines have become invaluable assets in streamlining industrial cleaning processes. As businesses continue to prioritize sustainability and efficiency, laser cleaning is poised to play a central role in shaping a cleaner and more sustainable future.
Revolutionary Automated Pipe Welder Streamlines Manufacturing Process
Automated Pipe Welder Revolutionizes the Welding IndustryIn a world where automation is becoming increasingly prevalent, the welding industry is no exception. The introduction of automated pipe welders has revolutionized the way pipe welding is done, making it faster, more precise, and incredibly efficient. One of the leading companies at the forefront of this industry-changing technology is {Company Name}.{Company Name} has been a pioneer in the welding industry for over two decades, specializing in the development and production of high-quality welding equipment. Their commitment to innovation and cutting-edge technology has led them to create the most advanced automated pipe welders on the market.The automated pipe welder developed by {Company Name} integrates state-of-the-art robotic technology with advanced welding techniques, resulting in a system that is capable of performing complex welding tasks with unparalleled precision. The machine's ability to work with a variety of pipe sizes and materials makes it a versatile solution for a wide range of welding applications.One of the most significant advantages of using an automated pipe welder is the dramatic increase in productivity. Traditional manual welding methods are time-consuming and require highly skilled welders to achieve the desired results. The automated pipe welder eliminates the need for manual labor, reducing the time and cost associated with welding processes while maintaining a consistent level of quality.Additionally, the automated pipe welder is equipped with advanced sensors and monitoring systems that ensure the weld quality meets industry standards. This level of precision and consistency is difficult to achieve with manual welding methods, making the automated pipe welder an attractive option for companies looking to improve the quality of their welded products.Furthermore, the automated pipe welder is designed with safety in mind. By reducing human involvement in the welding process, the risk of accidents and injuries is significantly minimized. This not only creates a safer working environment but also lowers the company's liability and insurance costs.In addition to the increased productivity and safety benefits, the automated pipe welder offers substantial cost savings. The reduction in labor costs and the efficient use of materials result in a higher return on investment for companies that adopt this technology. By streamlining the welding process, companies can complete more projects in less time and with fewer resources, ultimately increasing their bottom line.The impact of automated pipe welders extends beyond the manufacturing sector. The construction industry, for example, benefits from the use of this technology in the fabrication and installation of pipelines. The ability to produce high-quality, consistent welds in a fraction of the time compared to traditional methods makes the automated pipe welder an invaluable asset in large-scale construction projects.As the demand for automated pipe welders continues to grow, {Company Name} remains committed to meeting the evolving needs of the industry. Their dedication to providing reliable, efficient, and innovative welding solutions has solidified their position as a leader in the field of automated pipe welding technology.In conclusion, the introduction of automated pipe welders has significantly transformed the welding industry, and companies like {Company Name} are at the forefront of this revolution. Their state-of-the-art technology and unwavering commitment to excellence have set a new standard for welding efficiency, safety, and quality. As the adoption of automated pipe welders continues to expand, the future of welding looks brighter than ever.
Efficient and Precise Cutting: The Advantages of Pipe Cutting Lasers
Title: Revolutionary Pipe Cutting Laser Revolutionizes Industrial Cutting ProcessesIntroduction:In this era of rapid industrialization and technological advancements, the manufacturing sector has witnessed significant progress and innovation. One such groundbreaking innovation comes from an esteemed company, which has introduced a game-changing technology designed to transform pipe cutting processes. This technology, known as the Pipe Cutting Laser, has the potential to revolutionize the industrial sector by offering a highly efficient and precise cutting solution. This article aims to delve into the capabilities of the Pipe Cutting Laser and its potential impact on the manufacturing industry.Cutting-Edge Technology for Enhanced Efficiency:The Pipe Cutting Laser is a state-of-the-art machinery, integrating advanced laser technology with intelligent automation systems to provide unmatched precision and efficiency. With its ability to cut various types of pipes, including but not limited to metal, plastic, and composite pipes, this technology is a versatile tool that can cater to a diverse range of industries.Exceptional Precision and Accuracy:The paramount advantage of the Pipe Cutting Laser lies in its ability to deliver exceptional precision and accuracy. Unlike traditional cutting methods, which often result in imprecise cuts and irregular edges, the laser technology incorporated in this cutting system ensures clean and perfectly angled cuts. This precision not only boosts the overall quality of the end product but also minimizes material wastage, thereby promoting cost-efficiency for manufacturers.Streamlined Workflow and Time Optimization:The Pipe Cutting Laser embodies technological advancements that have expedited the cutting process significantly. With its intelligent automation system, the laser is capable of seamlessly executing intricate cutting patterns and designs, eliminating the need for manual intervention. This automation enhances overall workflow efficiency, reducing production time and increasing productivity, providing manufacturers with a competitive edge.Unparalleled Versatility:The versatility of the Pipe Cutting Laser sets it apart from its counterparts. Its cutting mechanism can be applied to pipes of varying diameters and thicknesses, making it an excellent tool for a wide range of industries, including automotive, aerospace, construction, and more. From fabricating metal pipes for aircraft manufacturing to accurately cutting plastic pipes for plumbing purposes, this cutting-edge technology offers manufacturers an unparalleled range of applications.Health and Safety Considerations:In addition to its technical advantages, the Pipe Cutting Laser also prioritizes the health and safety of operators and workers involved in the cutting process. Unlike traditional cutting methods that generate hazardous debris and fumes, the laser technology employed minimizes the emission of harmful byproducts. This feature not only improves the working environment but also ensures a healthier ecosystem for all stakeholders involved.Environmental Consciousness:The Pipe Cutting Laser embraces an environmentally conscious approach by significantly reducing material wastage. With its precise cuts and minimal kerf width, the laser technology optimizes material utilization, reducing the amount of scrap generated during the manufacturing process. By minimizing material waste, this cutting-edge technology aligns with sustainable production practices and supports companies' efforts towards environmental stewardship.Future Prospects and Industry Impact:The introduction of the Pipe Cutting Laser marks a significant milestone in the Industrial sector, fostering a new era of automation, precision, and efficiency. This technology presents endless opportunities for manufacturers to enhance their processes, optimize workflow, and improve the quality of their products. By leveraging this cutting-edge solution, industries can meet rising customer demands, cut costs, and remain competitive in an increasingly globalized market.Conclusion:In conclusion, the Pipe Cutting Laser's implementation promises to revolutionize industrial cutting processes, paving the way for enhanced precision, efficiency, and sustainability. This pioneering technology showcases the potential for transformative advancements within the manufacturing sector, benefitting a wide range of industries. With its exceptional precision, versatility, and focus on health and safety, the Pipe Cutting Laser stands as a testament to ongoing technological innovations that continue to shape the future.